Finish, Getting It Running, Dirty Old Parts
April 17, 2016
The game is up and running. There are some details to finish up.
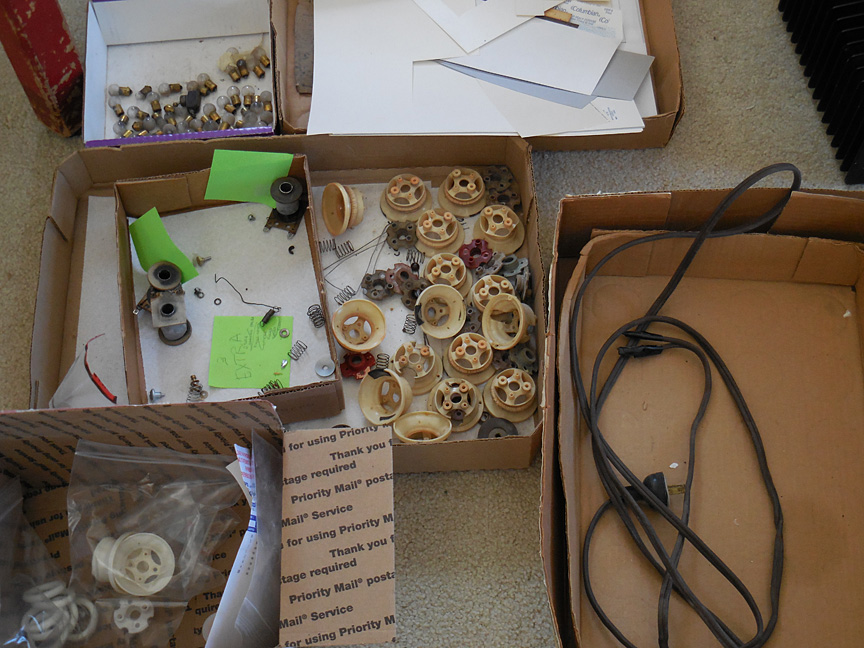
Here are the boxes of old parts and some new that were not used. Most of this stuff goes in the trash but some, like the springs, are retained. Some of the original parts that are difficult to find, equivalents like the coils, go in a bag in the bottom of the machine. Should someone want to restore this game after another 65 years, they will have some basis for replacing parts.
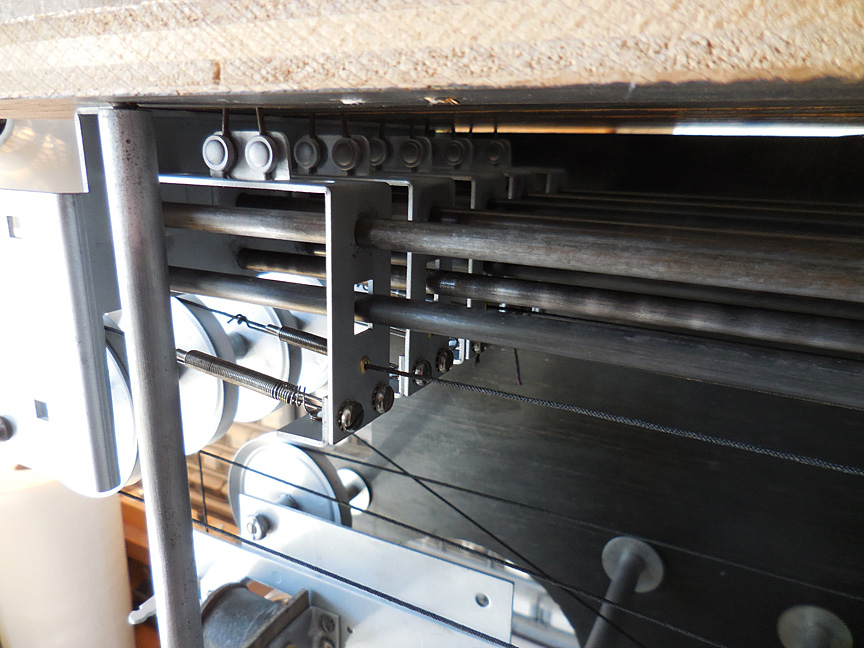
I started fixing the logic errors in the game. The design by United was poor and the technicians that needed to repair the games were challenged. I found several race conditions that should never be designed into the game. A race condition is one where several things are counting in a delay in a contact or a contact that stays closed for a long period while several other things are happening. The delay of completion of those things will cause errors.
One example was the hole kick outs. They need to wait for the game to count the number of moves for the horses. Should that delay take too long, the kick out is weak or even not working.
I had problems with the horses returning to the start for a new game. I try very hard not to used any lubricants in the game and prefer to make the mechanism clean. Any oil will attract dirt and grit which will slow the game and make it eventually fail. While the mechanism will work easily for a short time, it will eventually gum up and stop. A non-lubricated mechanism will work longer.
The horses were not returning to the start because of wear patterns in the tubes that locate the horse carriage. In the pictures above, you can see the wear pattern on the bottom tube, like a shiny and then dark area and repeat. I moved the heavily worn tube, previously located on the top, to the bottom. I also rotated the tubes so the wear pattern was on the bottom or top. The preload on the steppers is three turns and I was able to get the horses to return easily with some adjustment.
The game was a challenge to get working again. There were some particularly troublesome gremlins. The video above documents most of them.
I used a Variac to initially add power the the machine. The game just kept cycling as if a ball had landed in a kick out hole. The problem was a bumper wire soldered to the grounded end of the switch rather than the powered end. To the game it looked like a ball was always in the hole.
The kick out power was very weak. This was caused by the race condition mentioned above.
The horses were sluggish when they returned to the start line. The cause was the wear pattern in the rods that support the horse carriages. A quick adjustment had them eager to return for another race.
The knockoff button on the bottom of the cabinet had a broken tab. The glob of solder used to attach the wire shorted out the switch making it look like it was always closed. This caused numerous problems, some of them not associated at all with the source of the problem. For example, the game always knocked off any games won and then tilted. Tilting the game sent 30volts into the lamp circuit of the currently selected horse, burning out the lights. Of course, you could never win a game!
Once fixed, the game stored wins, allowed the replay button to work, and stopped burning out lights!
Another problem an eagle eyed observer of the video will notice is the occasional failure of the kick out to operate. This was again due to a race condition and an adjustment of the sequence wheel made them more reliable.