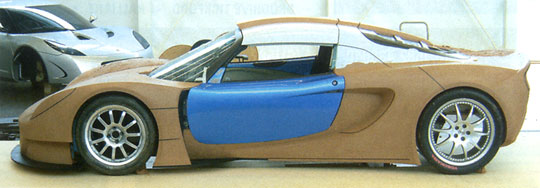
Sport Exige Racer styling clay shows considerable revisions over standard road-going version, principally in widened, more boxy front and rear arches and lower sill line. Almost none of the original car's panels were retained
Sport Exige, Body Building Exercise
Words: Charles Clarke
Photos: Lotus Sport
Racecar Engineering, September 2006
When Lotus was approached to build a one-off Exige racer in just six months, it required a new approach to established carbon fibre processes.
Lotus Cars has a reputation for producing excellent handling sports cars for the enthusiastic driver. It also has a specialist motorsport performance division called Lotus Sport that builds and maintains all the specialist racing versions of its cars for the various one-make series and for independent Lotus racers around the world.
Consequently, when the company was approached by a wealthy Lotus racer from South East Asia (who wishes to remain anonymous until his new car breaks cover) to design and build what can best be described as an extreme Lotus Exige racecar, the only question Lotus Sport asked was 'when do you want it?'
For most production vehicle makers, the 'in six months' reply would have been met with howls of laughter, but not at Lotus. In an environment where the solution to long lead times for new model introduction is addressed by total computer integration from day one, Lotus decided to go back to its roots and build this racer the more traditional way.
It assembled a minute design and manufacturing team so that effective communication was second nature and selected tried and trusted suppliers and processes to speed up problem resolution. And it opted for traditional styling processes (hand sketches and clays) that were directly linked to manufacturing to short circuit even the slick modern computer styling and production processes.
Key to the whole exercise was the inclusion of RTN (Racing Technology Norfolk Ltd), the team responsible for the Le Mans-winning Bentley, to produce the specialist lightweight carbon fibre bodywork that was to be mated to a standard, road-going Lotus Exige extruded aluminium and bonded chassis.
The Lotus Sport Exige racer is significantly longer (350mm) and wider (100mm) than its roadgoing counterpart to accommodate the larger, longitudinally-mounted engine and gearbox, wider track and longer wheelbase, as well as to optimise the aerodynamics. The length is mainly from the cockpit rearwards but the short rear overhang design of the road-going Exige is maintained in order to preserve what Barny Hatt, the designer, refers to as the Exige DNA.
Consequently, there was considerable redesign of the existing bodywork to accommodate the wider track and the racing powertrain. The Sport Exige racer required a new front clamshell, A-panel, body side outer and sill, roof, engine cover and rear clamshell, plus some specially developed aerodynamic parts like the rear wing and rear diffuser.
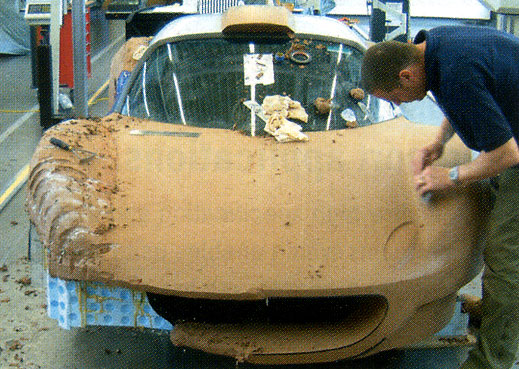
Carbon innovation
All these parts were made in lightweight ZPREG carbon fibre by RTN using an innovative mouldmaking process that featured room temperature curing. The moulds were taken straight off the Sport Exige styling 'clay' and the resulting carbon fibre panels were race ready without having to rely on the costly tooling usually associated with current carbon fibre technology. This is thought to be the first time that this technology has been used on such large panels.
'For dimensional stability, ambient temperature and pressure carbon pre-preg is a good idea,' says Graham Muff, composites manager at RTN. 'One of the challenges with carbon fibre composites is to retain the dimensional design intent whilst using elevated temperature and pressure to cure components. ZFREG still uses pressure to the extent that the components are sealed under vacuum after being laid up in the conventional way, and they can be cured at a low temperature in an ordinary oven rather than expensive, high-pressure autoclaves.'
Low temperature curing pre-pregs are made exactly the same way as conventional pre-pregs but have a resin chemistry that allows curing to be achieved at temperatures from 60-100 deg C. The flow profiles of the low temperature resin systems allow for the use of vacuum bag pressures alone, again avoiding the need for highpressure autoclaves.
ZPRFG is a selective resin impregnation technology developed by the Advanced Composites Group (ACG) for rapid lay-up and moulding of laminates using an oven/vacuum bag curing process. The material achieves high quality, pit-free surfaces and low internal voidage in all component types.
Whilst primarily aimed at 60 deg C oven! vacuum bag processes, the rapid lay-up benefits of the technology can also be used in autoclave or press moulding processes and can be adapted for shorter cycle time, higher temperature cures. In this instance RTN used a minimum temperature of 8odegC but preferred 120 deg C where possible and used its own autoclave at a vacuum bag pressure of only 14lb/in2.
ZPREG materials may be single fabrics or, more often, two specific fabrics laminated together. There are two types: ZPREG surfacing plies and ZPREG backing (or hulking) plies depending on the application. The surface ply usually consists of a lightweight fabric laminated to a dry, medium weight fabric using stripes of resin. The resin impregnates the lightweight fabric sufficiently to provide light tack, whilst the heavier inner fabric retains a dry surface. This format ensures air is channeled away from the tool face before the resin stripes close. The backing ply is usually formatted with heavier fabrics for rapid deposition, with resin stripes applied to one surface to provide a light tack for easy lay-up. Both the surfacing ply and the ZPREG bulk plies handle as if they were 'dry' unimpregnated materials giving excellent drape characteristics. This significantly reduces manufacturing times compared to resin infusion and wet lay-up processes. When compared to standard pre-preg processes, the reduction in laminating times can be as much as 70 per cent. However, in applications where surface filling and abrading has been a major cost element, it is the quality of the ZPREG surface finish that
potentially offers the greatest cost savings, so it is ideal for automotive class-A external surfaces.
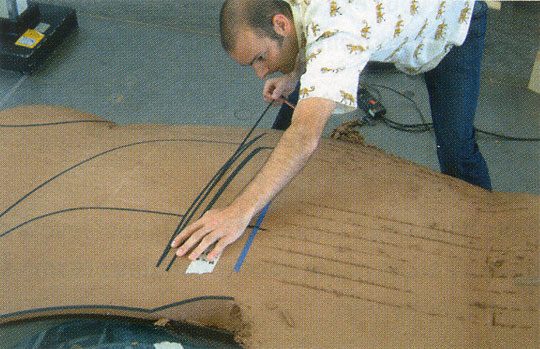
'Traditionally, if you were going to make a monolithic composite structure that was i.6mm thick with a regular pre-preg you are limited to relatively thin plies,' says Muff. 'For example, a 200g/mm pre-preg would give you around 0.25mm/ply and that would increase until you reach the 400g/mm range where the thickness is about 0.45mm/ply. In these situations there is obviously the labour cost for every ply you lay down to build up to 1.6mm. With the ZPREG BPS (body panel system) you only have two plies - a surface ply and a bulk ply.'
'If you used a monolithic carbon pre-preg with no syntactic core or fillers there is obviously more strength than the ZPREG because there are more fibres through the cross-section, continued Muff. 'But if you look at the ZPREG BPS literature, the idea with ZPREG is to replace a traditional 1.6mm pressed steel panel. So you would have a similar stiffness to a steel panel but with considerably less weight, but it wouldn't be structurally comparable to a full traditional pre-preg part that you would find in an H car.'
ZPREG was originally developed to replace steel with a view to win business from the steel body replacers or from those organisations wishing to shed weight in steel/composite body constructions. And by happy coincidence this technique is also very valuable for companies wanting carbon composite panels without the hassle, expense or inconvenience of using the traditional pre-preg autoclave method.
'We've not used it for structural components, only for bodywork,' Muff continues. 'The product has been around a number of years and has been re-formulated and improved. It's on its third or fourth incarnation now. And Advanced Composites have reportedly got another version on the way, which is "bigger and better" than the last one. For a specific weight, the new version will be stiffer or tougher. As time passes, these kinds of novel composites are continually improving. Eventually you will be able to specify design criteria like ply directions in the same kinds of ways and that you can currently specify with traditional pre-preg lay-ups. And you'll probably be able to get multi-axial (orthogonal and 45-degree) ply packs in a single pre-preg for structural use in the fullness of time.'
The normal process at RTN for making body panels from a clay model is to produce a mould by taking a plaster cast of the clay and making a plug (or heavy) from that mould and then making a carbon fibre mould from the plug. The clay is covered in Di-noc (which is a bit like resilient Clingfilm) and the plaster mould is made using proprietary products which use a gel coat and plaster system for making the initial mould.
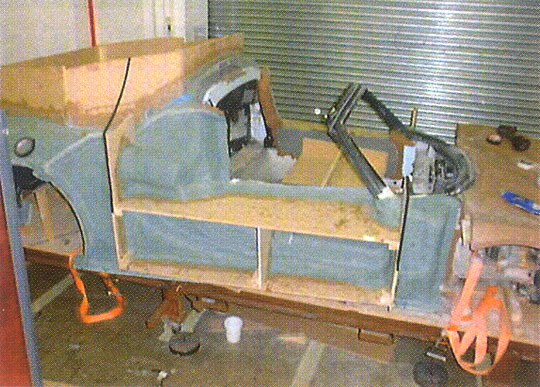
The plug is usually a wet lay-up in epoxy carbon fibre from the plaster mould and a carbon pre-preg mould is produced from that. By working with consistent materials ie making a carbon mould for a carbon panel, all the material movements are compatible. But at every generation you have potential dimensional instability and you are constantly resisting the temptation to warm up the process because with heat comes expansion or growth, especially with large panels.
Consequently, what RTN did with the Exige racer was to use the Axson Epopast 400 system. This allows you to work straight from the clay. As Muff explains: 'For this we 'released' the clay with liquid wax as you would for a plaster, but then we used the Axson gel coat and fibrous putty system to generate a mould straight from the clay. This cures at room temperature without a vacuum bag. It is like a short fibre dough mixture - you put it on in handfuls over the semi-cured gel coat and then roll it out as you would with a wet lay-up.
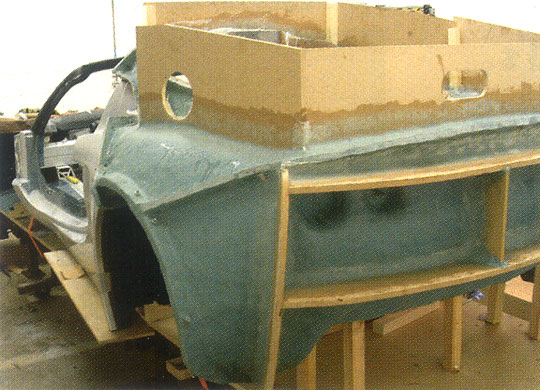
This gives a 10-12mm thick mould. You don't need special tools, just normal wet lay-up implements.'
The Epopast mould is relatively stiff as the fibres in the epoxy paste mix are 2o-3omm long. These fibres are very fine and you can mould it quite effectively and safely using the lightweight rubber or latex gloves. Once this epoxy paste is in place the whole thing is stiffened using a traditional 'egg box' backing structure made from MDF attached to the mould but isolated from it using silicon adhesive.
The mould is post cured at elevated temperature and then tested for surface integrity at elevated pressure (6opsi in the autoclave) and checked for dimensional accuracy. This produces quality mould straight from the clay that can be used directly for the ZPREG lay-up. Using this technique RTN cut two steps out of the process, which not only saved valuable time but also minimised potential errors.
'Once the styling had been signed off, we looked with the designers at the best way to split I he panels. These were marked up on the clay and moulded in stages as normal, to capture undercuts and so that the moulds came off easily.'
The Axson Epopast 400 material had been used in the past to make wind tunnel model body parts but it had never been used for moulding a full car. Everyone at Lotus was very happy with the dimensional accuracy -+/o.5mm on large composite body panels is good by anyone's standards. 'You can use this mould-making technique without elevated temperature and pressure which are always the 'gotchas' which stop weekend racers making more use of carbon fibre. Axson Epopast 400 is primarily sold for moulds to the ceramics industry, or as backing for RIM tooling, so nobody had really exploited the product or looked at the possibility of making full vehicle panels using the technique. It's not a volume seller like epoxy tooling block.'
RTN identified the material some time ago and thought it looked interesting. 'When we got the commission for the LSE racer body we thought there was a perfect fit for this product in this project,' Muff continues. 'What we didn't have plenty of was time, so it made sense to use this technique, especially since we had an accurate clay. If we had gone the traditional route of digitising the clay, CAD modelling and CNC cutting mould tools it would have taken much longer.'
With such a tight build schedule, the car was run only briefly in the workshop, with a short lowspeed systems check and a high-speed shakedown test at the Lotus test track by former Lotus Fi driver Martin Donnelly. Once baseline set-up had been established, the car was crated-up and flown to its owner in South East Asia for local development prior to starting the racing season in June of this year.
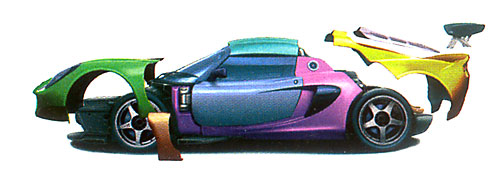
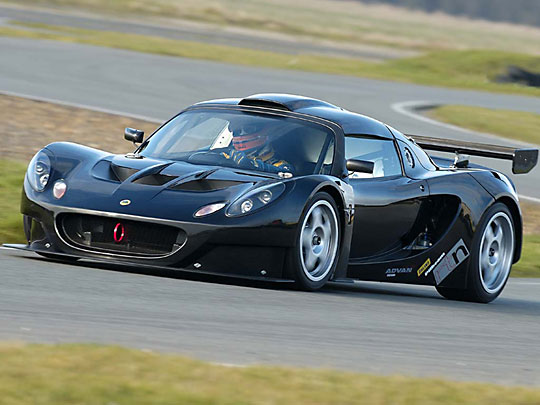
Chassis and suspension | Bonded and extruded aluminium chassis weighing Engine 68kg and with a torsional stiffness of 1 0,500Nm/ degree | |
FIA approved eight-point rollcage, fitted prior to the bodywork | ||
Double wishbone front suspension with the same pick-ups as the road-going Lotus Exige | ||
Rear suspension pick-ups on revised rear subframe, fully adjustable for ride height, camber and castor | ||
Adjustable front and rear anti-roll bars | ||
Coil springs mounted over Ohlins ST44 three-way adjustable dampers front and rear. | ||
AP Racing three-point air jack | ||
Brakes | AP Racing pedal box with brake balance bar | |
AP Racing six-piston front calipers and four-piston rear calipers | ||
No ABS | ||
344mm vented front discs 330mm rears | ||
Wheels and tyres | OZ Racing Chrono one-piece cast magnesium rims (8.8Jxl 7 ET4O front and 11 .2SJxl 8 ETSO rear | |
Yokohama tyres (250/610-17 front and 280/650 Aerodynamics | ||
Engine | Naturally aspirated, narrow-angle, 24-valve, 2998cc GM V6, tuned by Swindon Racing Engines, mounted longitudinally and weighing 157kg | |
Bore | 86mm | |
Stroke | 86mm | |
Fl-style airbox and air snorkel from the roof panel feeding directly into six carbon fibre air trumpets | ||
Dry-sump oiling with oil-water heat exchanger and water cooling | ||
Management | MoTeC M600 | |
Power output | 400bhp (296kW / 4O5ps) at 7750rpm | |
Torque | 2941b.ft (398Nm 40.6kgm at 6500rpm | |
Maximum engine speed | 8250rpm | |
Power-to-weight ratio | approximately 410bhp/tonne (0.351 kW/kg/476ps/tonne | |
Transmission | Single mass stepped flywheel | |
AP Racing twin-disc cerametallic race clutch | ||
Hewland NLT sequential six-speed dog-type transmission with in-line shift mechanism, cooled by an oil-water heat exchanger | ||
Limited slip differential with separate power and brake ramp angles | ||
Aerodynamics | Front splitter | |
Carbon fibre rear diffuser | ||
Adjustable carbon rear wing | ||
Miscellaneous | Stack display with integrated data recording | |
Raychem 25 wiring system with Beru Mil-spec connectors | ||
Conventional fuses replaced with circuit breakers | ||
Single racing bucket seat mounted as right-hand drive to optimise weight balance | ||
Six-point seat belt | ||
HANS safety system | ||
Removable quick-connect steering wheel | ||
100-litre FT3 safety fuel cell with quick re-fuelling system mounted between driver and engine | ||
Fully plumbed electrical fire extinguishing system
|
photo caption for suspension picture: Double wishbone front and rear suspension was designed by Lotus Sport and fabricated by Pilbeam. Sport Exige also has adjustable anti-roll bars, Wins three-way adjustable dampers and AP Racing brakes.
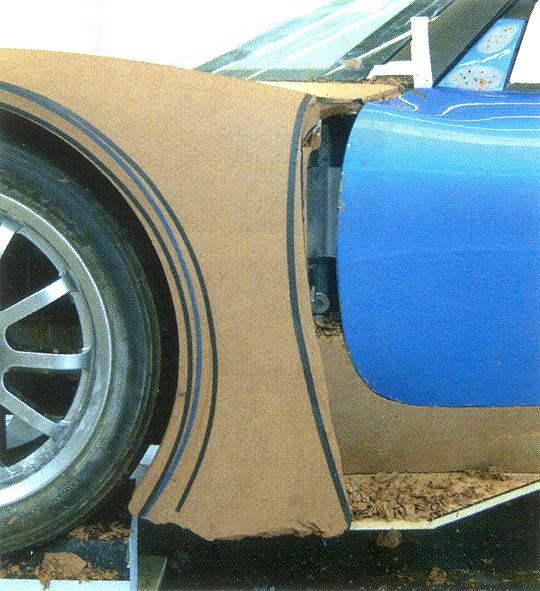