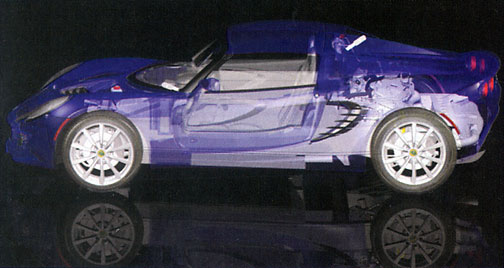
Reengineering the Lotus Elise
The company hopes the re-engineered Elise can out-maneuver its competition by showing the importance of performance through light weight
By Kevn Jost
Automotive Engineering, October 2004
In July, Lotus began exporting to the U.S. a Federal version of the Elise-nearly a decade after it introduced the vehicle to other world markets. The first new Lotus model for the United States since 1991, the Elise is spearheading the company's market expansion plans in America.
The Elise has been the best-selling Lotus ever, with about 20,000 units sold worldwide since the original Series 1 (SI) hit the UK market in 1996. That is nearly double the total sales of Lotus's longest-running car, the Esprit, which completes production this year after a 26-year run. The company expects to sell roughly 2200 Elises in the U.S. in its first full year, a significant increase from the 100-unit per year sales volume of the now-defunct Esprit.
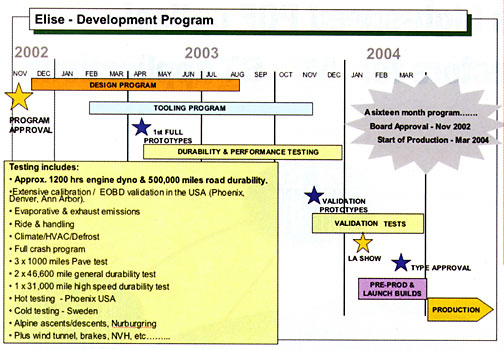
16-month program
The S1 Elise was conceived as a low-volume boutique model for Europe, but overwhelming demand delayed the start of development for a U.S. model, says Lotus. The Federal Elise program also had to wait until parent company, Proton, which held an 80% share of Lotus, obtained full ownership of the company. "Essentially that was the bit that took the longest time," said Roger Becker, Senior Consultant-Vehicle Engineering, Lotus Engineering.
Becker put the Federal Elise program together, doing the foundation engineering and market research. He also made the business case for the car coming to the U.S., "and kept on making the case until it was heard," he said.
It wasn't until November 2002 that approval came for the program, code-named Croft after a racing circuit in the UK.
The 16-month program culminated in pilot production in February 2004 and start of series production in March 2004. In comparison, the relatively simple, original Elise for Europe was delivered from a clean sheet of paper to production in 24 months, said Becker.
Along with the new Federal Elise came new development process. "We realized a few years ago that we needed to be more process-driven," said Becker. "Each project in the past was a new adventure. We had to turn an adventure into a proper business venture, and the only way to do that was through a controlled process. On this car, [the new process] has proved its worth in gold because it forces everything to be transparent.
"We're very proud on the engineering side of the business that the program is pretty compact," said Clive Dopson Manufacturing Director for Group Lotus, who had engineering responsibility for the Federal Elise program and its European market sister program, the Elise 111R.
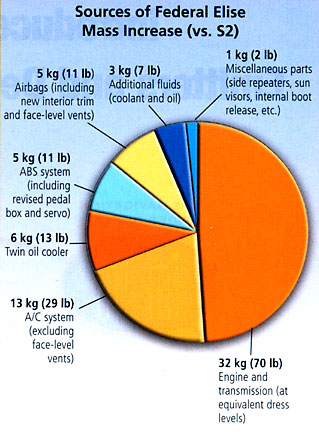
Performance through light weight
Reflecting the 52-year-old company's history of innovation and founder Colin Chapman's desire to build sports cars that adhere to his mantra of "Performance Through Light Weight," the two-seat roadster combines a 190-DIN hp (139-kW) Toyota four-cylinder engine-instead of the European car's Rover-based unit, which continues in production-with an overall vehicle mass of less than 2000 lb (907 kg) for an extraordinarily fun-to-drive experience. The Elise has a 0-60 mph (0-97 km/h) acceleration time below 5 s and a top speed of almost 150 mph (240 km/h), but EPA fuel economy is an impressive 26.1 mpg in the city, 37.5 mpg on the highway.
During the early days of the original Elise development program, Lotus was unable to find a suitable technology to produce a lightweight and exceptionally rigid structure, so engineers looked outside the automotive industry and brought together aluminum extrusions and aerospace bonding techniques. That groundbreaking epoxy-bonded aluminum tub chassis technology is still used today. The individually extruded chassis parts are bonded using epoxy resin adhesive, which Lotus says achieves exceptional strength and the ability to absorb extreme loads. Lap instead of more traditional butt joints provide a better bonding surface, and EJOT flow form fasteners further increase the structural integrity by reducing material "peel" in severe impacts. Chassis modifications in 2000 included lower, reinforced longitudinal sills to improve cockpit access.
For the Federal Elise, the tub chassis has changed only in detail. Despite being extremely light, the Elise's structure, which includes a composite energy-absorbing front crash structure, is tough enough to meet all U.S. government crash standards. The body is made from closed-mold composite material that is thinner and lighter than the original's hand-laid glass fiber.
With the original Elise, "'performance through light weight' was really brought to bear," said Becker. "Tony [Shute, the original Elise's Program Manager and now Lotus Cars'Head of Product] argued every gram on that car, and it was the right thing to do at the time. We wanted to deliver a pure, out-and-out performance car, and because we didn't have a lot of horsepower, light weight was absolutely critical to the car. We knew innovations using new materials and keeping the car simple was really important at that stage."
The new Elise is more complicated and carries a lot more equipment, but that is what the market demands, said Becker. The target curb mass for the Federal Elise was 900 kg (1984 lb), with actual base specification production cars coming 5 kg (11 lb) under target at 895 kg (1973 lb) full of fuel. This compares with the Elise S1’s curb mass of 760 kg (1676 lb) and the S2's 830 kg (1830 lb). The Federal Elise's 65-kg (143-1b) mass increase over the S2 version comes primarily from 32 kg (70 lb) more for the engine and transmission and 13 kg (29 lb) for the A/C system, said Nick Adams, Federal Elise Vehicle Development Manager.
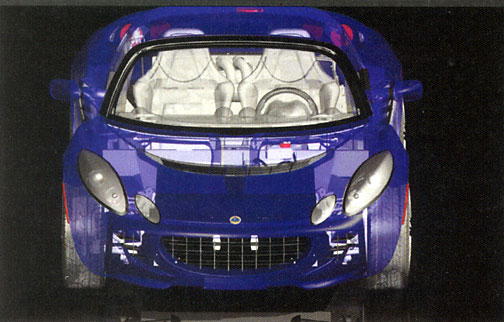
Safety and emissions
"The most challenging parts of this program were undoubtedly the combination of meeting crash testing requirements for the Federal market for the unbelted occupant and meeting U.S. emissions standards, within the constraints of the program timing," said Adams. "We've achieved full compliance with the NHTSA safety standards for the unbelted occupant, which we are very proud of; in a car this size, that is quite an achievement."
In addition to changes to the powertrain and safety systems, "all the market research said that a certain level of equipment had to be standard as part of the expectation of the U.S. customer," said Becker. "Air conditioning was one, ABS another. It was kind of 50:50 on electric windows and central door locking." All but electric windows are standard.
External design changes from the S2 include sidemarker lamps on the front and rear fenders to meet government requirements, the shorter exhaust pipes now exit through the rear under-car diffuser to save 2.5 kg (5.5 lb), and the sports-pack wheels are new. Adams says those new machined, forged wheels achieve an exceptional strength/mass ratio and are believed to be the lightest CIE wheel available in the U.S.
The biggest interior changes are the result of the fitment of airbags. The Siemens frontal airbags are now housed in a new Momo steering wheel and new instrument panel (IP), the latter now consisting of a skinned polyurethane top portion with the remainder an injection molded PC/ABS blend. (The previous IF was made of vacuum-formed sheet ABS.) The driver's side airbag is said to be the world's most compact. Air conditioning was introduced on the S2, but it is now much better integrated with the new IP. Interior ergonomics are also better now, with the radio in the center of the car rather than on one side.
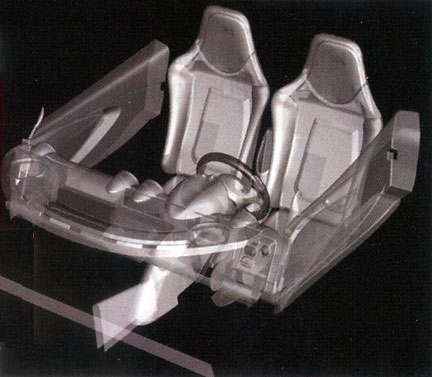
The Federal development team was led by a small group of engineers from Lotus Engineering. "From an engineering point of view, we had a core team of about 12 people, with individuals responsible for discreet areas of the car such as powertrain, body, and chassis," said Adams. Added Becker, "We operated on a matrix system, where the major controlling influence is that of the release engineer, of which there were about a handful." In total, about 50 people worked on the program, according to Adams.
The first full prototypes were up and running in April 2003. "Since then, we have been running the most detailed development and validation programs we've ever run on our own product," said Dopson. "Most of the testing involved with the program dealt with calibration, primarily of the engine control unit."
The testing and development program for the Federal Elise and the Elise 111R involved more than 500,000 mi (805,000 km) of road testing throughout 2003 covering a range of climates from the Arctic Circle, to the Arizona and Nevada deserts, and at altitude in Colorado. "Nearly half of the durability testing was done at the vehicle's top speed of 150 mph," said Dopson.
Dopson is pleased with the results. "During this program particularly, we've been very focused on the fact that there has been a very integrated approach between engineering and manufacturing teams," he said.
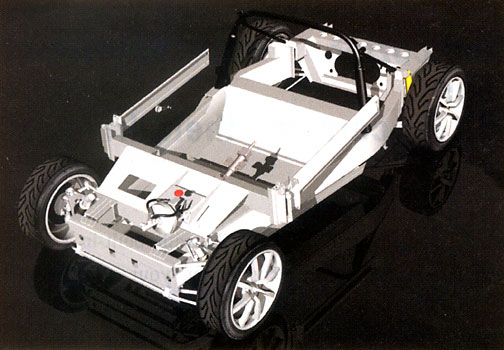
Refined ride and handling
The most significant change to the Federal Elise chassis is a new rear subframe to accommodate the Toyota powertrain. The galvanized steel unit, which also includes the rear suspension attachments, is much larger and more rigid than that of the European car that uses the K-Series engine. In contrast to the aluminum chassis, galvanized steel was used for the subframe because it allowed for a smaller and lighter structure. The subframe connections are much stronger but a little heavier, for improved torsional rigidity.
In terms of chassis engineering, Dopson is most proud of the Elise's ride and handling. "The early [SI] car had a reputation for being harsh on potholes. We took out that harshness. We've learned about compliance of the structure and suspension, which has allowed us to keep fine-tuning, getting the torsional and axial compliance performance of the bushings exactly in tune with what we wanted."
The Elise features four-wheel independent suspension with wishbones at each corner and Eibach coil springs and Bilstein monotube gas dampers all around.
"The biggest change we made to the suspension is to damper settings and spring rates," said Adams. "On the standard suspension, we've increased the spring rates over the European car by 20%." Along with the spring revisions, Lotus engineers revalved the dampers, altered the rear suspension geometry by moving the pickup points slightly outward for the bottom wishbone, and revised the antidive and anti-squat geometry slightly.
"Matt Becker [Principal EngineerVehicle Dynamics] has exceeded our expectations," said Adams. "We thought we would manage to get a ride-and-handling balance that was close to the European car's, but it is actually superior due to the revalved dampers."
Compliance with freeway hop, caused by the unique concrete-slab roads in the U.S., is improved with altered bump and rebound settings, particularly of the front dampers. "The European damper settings in the States were quite unpleasant; you got quite a choppy ride," said Adams. "It's always a bit of a compromise, though, because as we soften up the damping at the front a little bit, what we tend to do is lose some steering response. And, obviously, steering response is everything we're about."
So Lotus engineers worked hard to find the right compromise. "We've sharpened up the steering response rate of the tires to allow us to soften up the steering response due to the dampers," Adams said. Engineers are working to adapt the setup for European cars.
The tires are a big contributor to handling and road holding. Designed in conjunction with Yokohama, the Advan Neova AD07 LTS tires have a unique construction and compound specifically for the Elise. "Because the Elise is so light, we can't use off-the shelf tires because they just don't generate sufficient contact pressure," said Adams.
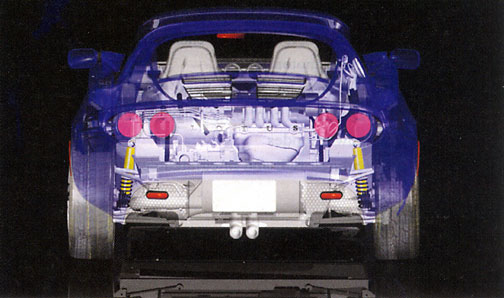
Lotus control for Toyota powertrain
Before the program officially began, Lotus engineers undertook a thorough evaluation of a range of power trains to satisfy their need for U.S. emissions compliance.
After first being turned down by Toyota, Becker was able to convince its executives to let Lotus use the 2ZZ-GE 1.8-L four-cylinder 16-valve VVTL-I engine as well as the C64 six-speed gearbox. Critically for Lotus, the engine is lightweight thanks to a compact metal-matrix composite alloy cylinder block. The mid-mounted, transverse unit is naturally aspirated with double overhead camshafts and hydraulic tappets. The all-aluminum six-speed gearbox was specified with the closest ratios and gearset available from Toyota. The engine-management system, bifurcated exhaust downpipe, and gearshift mechanism were developed by Lotus.
The VVTL-i system allows the engine-management system the flexibility to select the optimum camshaft profile, lift, and timing across the engine's operating range. The result is more linear torque output peaking at 138 lb * ft (187 N * m) at 6800 rpm, with peak power of 190 DIN hp or 186 SAE hp (139 kW) at 7800 rpm.
Due to the fitment of the higher output engine, and to offset the higher ambient operating temperature in the U.S.-the European Elise was rated at a 30'C (86'F) maximum operating temperature the Federal car's hood-mounted radiator exit was modified to effectively increase its area by 17% and improve cooling capacity by a commensurate amount, said Adams.
The biggest powertrain challenge for Lotus engineers was development of the engine-management system. "It was a potential deal breaker with Toyota if we weren't able to prove that we were capable of developing our own engine-management system," said Becker. But they were confident because "controller development is one of Lotus' core competencies," said Adams.
Lotus had a U.S.-market Toyota Celica shipped to the Lotus factory, where calibration engineers "replaced the existing controller with our controller, did a bit of firmware development and software calibration work," said Becker.
"The team that worked on the engine-management system comprised eight engineers from an engine-management group that's comprised of about 25," said Adams. Engineering of the T4 32-bit EMS software and much of the calibration and validation work was meant to ensure a smooth transition between camshaft profiles. And a CAN-based link between the EMS and instrument cluster reduces complexity, Adams noted.
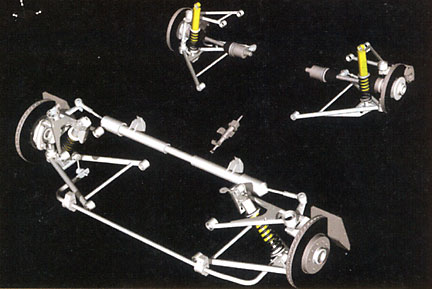
Enthusiast-tuned ABS
The braking system gained a servo for power assistance and an ABS system courtesy of TRW, allied with twin-piston aluminum front brake calipers from AP Racing and single piston rear brake calipers from Brembo.
The ABS was designed to enhance safety without compromising driver enjoyment, making "the braking one of the best parts of the car," said Dopson.
Lotus engineers wanted ABS operation to be subtle and trigger, right at the braking system's limits. What makes this possible is very subtle tuning of the algorithms that control the ABS cut-in point.
"When we got the ABS pretty well sorted, we sent Matt [Becker] out on the Nurburgring on a really hot lap. When he came back in, we asked him how many times the ABS triggered. He didn't think it did at all, but in reality the datalogger in the car said it triggered about 20 times."
Many Lotus engineers worried that ABS would take some of the fun away from driving the car. "Well it doesn't, because the ABS cuts in only when it has to," Adams said. "As far as the old argument that I can stop a car quicker than an ABS system can, well you'd need four feet to do that because it's a four-channel system. And you'd need four brake pedals as well. If a wheel starts to lock, it'll back the brakes off to that wheel and the remaining three will continue to be braked fully. So the old guys who say 'I can beat an ABS system' are sadly behind the times. It's not possible any longer."