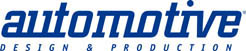
http://www.autofieldguide.com
Lotus Bonds with Aluminum
By Kermit Whitfield, Senior Associate Editor
If aluminum-intensive cars are ever to become more than an occasional curiosity, automakers may have to give up their weld shops. At least that ?s the conclusion you could draw after talking with the people at Lotus Engineering (Hethel, England). Lotus has been building cars with aluminum chassis for many years, but none of them are welded: they are held together with screws and adhesives. When Lotus first introduced the method on the low-volume Elise in 1996, company leaders were worried about market acceptance for what is essentially a glued-together car, but the technique proved so successful (over 23,000 cars produced with no reported failures) that it has become the basis of a new higher volume venture that may help to bring aluminum-intensive vehicles more into the mainstream. The new project, which uses Lotus ? Versatile Vehicle Architecture (see AD&P February 2004, ?Lotus ? Versatile Venture ?), tweaks the lessons learned on the Elise for volume production, but remains true to the fundamental concept: to get the most out of aluminum structures you must design for the material, not treat it like a steel substitute.
Bond, Adhesive Bond. First and foremost, that means not welding it. Why? ?The yield strength of aluminum goes down by half once its welded, ? explains Richard Rackham, vehicle architect at Lotus. So, getting the same strength in a welded aluminum chassis as in a bonded unit requires doubling the amount of material used; since aluminum is usually chosen for its light weight, that dilutes its key benefit. Another big disadvantage of welding aluminum is that stresses are localized along a point or a line, which can lead to material fatigue. Stresses are distributed over a wide part-mating when bonding is used. To gain the full merits of using adhesive, Lotus had to come up with ways to optimize its properties. For example, after determining that the optimum bond gap between parts is 0.2 mm, the question became how to maintain that gap uniformly over the bonded surface. The answer: Lotus designed tiny protrusions, or ?pips ? on the parts that held them exactly 0.2 mm apart.
![]() |
The shape of things to come? Lotus is bringing the aluminum bonding methods it pioneered with the Elise chassis to higher volume production. The first of the new vehicles are scheduled to be produced at the end of 2005. |
To fabricate the main chassis components Lotus chose a process well-suited to aluminum: extrusion. Chassis supplier Norsk Hydro ASA (Oslo, Norway) extrudes the closed-box parts out of 6000 series aluminum and bonds them to folded sheets of recycled 3000 series. Rackham says that one reason extrusions were chosen is because they can be inexpensively produced (he estimates the cost of a die at about $5,000), which helps to offset the higher material costs of aluminum. Another is that they can be formed into complex shapes that serve multiple purposes and help keep parts count down. The proof: the entire Elise chassis consists of only 27 different extrusions.
Higher Volume. The challenge Lotus now faces is translating the aluminum production methods for an essentially hand-made $40,000 sports car to affordable vehicles that can be mass-produced. It ?s current initiative, which is being conducted for an unnamed automaker, looks to build sub-$30,000 vehicles in the 40,000 to 50,000 annual unit range. To do that, Lotus is making some changes. According to Kerry Osborne, principal engineer, the hand-applied flow drill screws that are currently used to knit the Elise chassis together are being replaced by self-piercing rivets which can be shot more quickly, though they require application tools that generate at least five tons of pressure. But perhaps the biggest change is in the bonding. Realizing that no mass-production operation can afford the Elise ?s 50-minute curing time (nor would it wish to incur the expense of multiple ovens), Lotus is replacing the heat-cured single part epoxy adhesive used on the sports car, which required temperatures of 180°C, with one that will cure in the lower heat of the paint oven. (Both adhesives are sourced from Dow Automotive [Auburn Hills, MI].) The savings in process time garnered by these changes could be enough to peak the interest of volume automakers and get them to consider bonded aluminum chassis as a viable alternative for niche vehicle production. After all, what do they have to lose, except their weld shops?
Almost Ready For Prime Time
The initials QPF sound like they belong to yet another quality protocol, and ?in a way ?that ?s true. But the real words behind those letters are ?Quick Plastic Forming, ? and apply to a method for creating lightweight aluminum panels with greater styling flexibility and simplified assembly on low-cost single-sided tooling. ?QPF has been in development for six years, and we have 40 patents that are either issued or pending, ? says Alan Taub, executive director, Science Laboratories, GM Research & Development. ?Our process is adapted from a hot-blow-forming aluminum process used in the aerospace industry, and applied to mainstream automotive volumes and costs. QPF is designed to produce approximately 100,000 parts per year, versus a few hundred or thousand for conventional hot-forming.?
![]() |
One of two QPF cells at GM ?s New Hudson, MI, plant. |
GM ?s Metal Fabricating Div. has two QPF cells producing liftgates for the Malibu Maxx at its New Hudson, MI facility. If QPF had not been used, the liftgate would have had a pressed steel inner and outer covered by an SMC exterior panel, and a weight of 39 lb. The aluminum QPF panel, in contrast, uses single sheets of 5083 aluminum to create the one-piece inner and outer panels, and weighs just 20 lb. ?The 5000 series aluminum has a fine grain structure, which makes it more amenable to this process than current 6000 series aluminum sheet, ? says Mark Verbrugge, director, Materials and Processes Lab, GM R&D. He suggests that GM would like to expand the process to include the higher series, and that an enterprising aluminum company that solved this problem might see a marked increase in aluminum use. Verbrugge also says the process can be used with magnesium or titanium sheet, a potential boon for the aerospace industry.
In the QPF process, an aluminum sheet is resistance heated to 450ºC to 500ºC (the temperature at which it starts to sag) before being transferred to the hydraulic forming press. A high-pressure air stream causes the panel to conform to the shape of the one-sided die ?they are pushed into the die for more consistent grain movement ?and the still-hot panels are then transferred to a cooling fixture: there ?s minimal springback. ?A lot of effort went into the transfer of the panels, ? says Taub, ?because the part can be easily deformed at this stage. ? The heating and cooling of the aluminum contribute to QPF ?s two-to-five minute cycle time, one of the factors that mitigate against its use in volumes above 100,000 units per year. ?It would take a compelling styling or parts integration situation to add the tooling necessary to go above that volume level, ? says Taub.
With what Taub describes as a ?sweet spot ? for the technology at volumes up to 60,000 units per year, and more models entering the market at annual volumes of approximately 50,000 units, the future for QPF appears to be guaranteed. However, Taub and his team are quick to pa int it as just another tool in the toolbox for planners to draw from when deciding how best to produce a new vehicle. But it ?s a casual claim by Taub, made almost in passing, that makes you wonder if there is more to this technology than meets the eye: ?We could make the whole body structure of a vehicle out of 10 to 15 parts using this forming method. ? A concept vehicle built in this fashion is under discussion. Can a production vehicle be far behind? ?CAS
Automotive Design & Production, autofieldguide.com and all contents are properties of Gardner Publications, Inc.
All Rights Reserved.