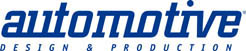
Lotus' Versatile Venture
By Kermit Whitfield, Senior Associate Editor
Versatile Vehicle Architecture is Lotus Engineering’s attempt to take platform sharing to the next level and allow automakers to make unique vehicles with high commonality and lower investment. If it succeeds, there could be a lot more funky low-volume vehicles in the marketplace.
A few years ago, Lotus Engineering’s (Hethel, England) leaders were casting about for holes in the automo- tive market that they could profitably fill with their engineering services, when they realized that though there was demand for low-volume niche vehicles like their own Lotus Elise, the investment needed to produce vehicles at annual volumes of only 10,000 to 15,000 units was prohibitive to all but a handful of makers. The problem was that there was no good way to make unique and appealing cars at those volumes and not charge exorbitant prices to cover costs. However, after a bit more research Lotus found that at volumes of 40,000 to 50,000 units, economies of scale would kick in that make it feasible to profitably build a sub-$30,000 car. But here’s the rub: at those higher volumes, production would far outstrip demand.
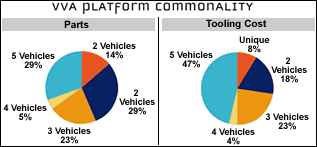
The driving force behind VVA is allowing automakers to get more bang for their bucks when it comes to platform sharing. These graphs show exactly how much Lotus thinks can be shared between different platforms.
The solution was to design a platform with a high degree of parts commonality and shared investment that could be the basis for three or four unique vehicles that would together reach the magic volume. Lotus could sell the concept to either a group of niche makers who would share the investment and each gain a unique vehicle, or to a giant car company with many nameplates looking to launch buzzworthy products in each of its lines. But to make the business model work, Lotus had to create a vehicle architecture that could morph into truly different products, not just thinly disguised sister vehicles. The development has become known as VVA: Versatile Vehicle Architecture.
Cornering. “Early on we came to the realization that the key was using corner units,” explains VVA program director Nick Sampson. The units he’s talking about are aluminum castings that sit at the four corners of the passenger compartment and serve as organizing points for the VVA design. Sampson and his team took the original idea from the Elise, and then experimented with different materials and designs. While they were in the midst of this experimentation, a customer signed on to the project who wanted an aluminum design, so development moved in that direction (though Sampson is quick to point out that steel is also perfectly feasible). With these four anchor points in place, Lotus hoped to create a platform that could accommodate a variety of body styles and powertrain layouts while maintaining high commonality. “We drove a lot of the complexity of the overall design into the corner units and they are absolutely common for every vehicle,” says Sampson.
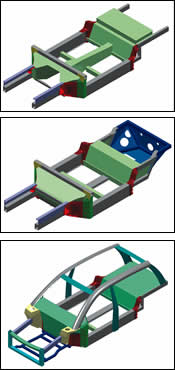
Lotus' VVA concept uses complex corner units (shown in red) to anchor a platform that can underpin everything from a mid-engine sports car to a 4WD SUV while maintaining high part commonality.
The acid test for the VVA platform was whether it could cost-effectively accommodate radically different layouts, so the team designed three variants of the platform: 1. front-engine rear-wheel-drive with four-wheel-drive, 2. mid-engine rear-wheel-drive, 3. Rear engine rear-wheel-drive. They found that not only could the VVA support all of the layouts, but that the stability provided by the corner design allowed them to markedly vary design features like front and rear length and overhang. This ability expanded the parameters of the vehicles that could come off of the platform not only from the point of view of styling, but in more down to earth ways like maximum weight, since heavier vehicles would need more impact absorbing space in their front ends.
Bonding. The next step was to decide on joining technologies. Both spot and MIG welding were studied and rejected partly out of concern for the degradation of the aluminium’s properties during the welding process. The VVA team leaned toward using self-piercing rivets to join components, but after testing the method under impacts and torsion loads found that the rivets alone wouldn’t be enough. Adhesives were also tried. Lotus had plenty of experience bonding vehicles together since it had been doing it with the Elise for years, but the sports car’s bonding agent requires pre-treatment of the aluminium and an oven-curing process that took too much time and investment to be cost-effective for the VVA concept. In the end, Sampson and his team found that the most efficient solution was a belt-and-suspenders approach that combines both self-piercing rivets and a cold-cure adhesive.
Sharing. The original targets for VVA were 30% parts commonality between vehicles and 50% common investment, and as of now projections are hitting those numbers. But the trick will be maintaining that high level of cost sharing as the project faces the inevitable pressure of ensuring that each vehicle is different enough from the others. Currently, in addition to maturing the core platform, Lotus is designing two variants for an unnamed customer and Sampson says his team is on track to put its first vehicles on the road around the end of 2005. He expects that the VVA’s basic technologies could have a development shelf life of up to 15 years, but acknowledges that since the target is the trendy niche market, Lotus may have to re-think the concept much sooner than that. As to whether VVA will ever become a mainstay of Lotus’s business, Sampson thinks not.
Automotive Design & Production, autofieldguide.com and all contents are properties of Gardner Publications, Inc.
All Rights Reserved.